小米首款汽车 SU7 搭载的核心部件及技术是否先进?有哪些值得关注的点?
雷军在本周发布了小米汽车的技术发布会,展示了包括在电驱、电池、大压铸、智能驾驶、智能座舱五个核心领域的突破和主要技术要素。这些相关议题连续霸榜了多日多平台的热搜头条。可惜我作为一个汽车产业的技术人员,这个时候的主要工作是做年底总结和新年计划,所以到今天这个假期,才有机会聊一聊小米汽车的这场技术展会。在过去的几天很多媒体、技术人员甚至主机厂的高管都加入到了这些技术亮点的讨论,有认可小米汽车亮点优势的,当然也有认为这里面依托了很多是供应商的技术突破,从而对小米汽车的自称自研颇有微词。关于这一点,我想说的是:新技术上限刷新的前提,首先来自于主机厂的产品定义。例如现在说到的高速电机,首先来自于小米对于su7的定义是要实现赛道级265kph的高速,那么在相同的结构下,更高的车速需求就需要电机适应更高的转速,除非你设置更加复杂的多挡结构。这是促使小米汽车去寻找能够支持突破转速上限电机供应商和挖掘自身合作研发实力的原始动力。再比如使用宁德时代麒麟电池倒置布局,其核心目标是在轿跑造型下布置超过100度电池的同时必须满足极限的电池包高度,只有这样才能在离地间隙、车内空间和维持低趴轿跑造型中得到妥协。首发应用,整车集成的联合开发技术难度很多时候不亚于零件自身的突破。简单来说就是第一波趟整车集成标准改变和测试验证的雷的就是首发主机厂。我们也注意到小米对周边技术和具体的方案也进行了大量的知识产权保护的工作,这也从侧面显示出这个是联合开发,而不是简单借用。所以,我觉得我们更应该关注和讨论的是,电动汽车高达265kph的高速性能冗余对于客户的价值如何挖掘,这种既要维持轿跑和低风阻造型又拼了命去应用最新的技术去挤出空间这种整车定位,是否真正抓住了米粉群体的爽点。所以小米汽车发布之后,我们知乎VIP创作者群里面马上就在艾特社区负责人,赶紧搞一辆知乎体验官试驾,在此我也呼吁小米汽车如果看到这篇文章,请考虑与知乎汽车合作。我在2019年1月去蔚来汽车内部交流的时候,我问过:为什么你们要首发ES8这款大七座但又续航里程只有355km的车型。因为当时的电池能量密度技术有局限性的情况下,ES8为了满足和后来的ES6共用电池包换电而牺牲了一大块空间闲置。也就是说,明明蔚来可以先首发看起来更加具有性价比的ES6,但是依然决定先冲ES8。蔚来高管的回答其实很直白,正如一开始要先打EP9一样,一个新品牌的首发车型就如同第一印象一样,决定了品牌的格调和定位。汽车品牌从高端做大众品牌容易,从低端向高端做更难。尤其是对于电动汽车这种破坏性创新的品牌,冲击颠覆高端对于销量的挑战有些大,但是对于品牌长期的价值留下了更大的空间。由于目前Su7的售价还没有公布,大家还在争议和猜测,但是Su7的赛道级高性能引发的品牌价值塑造和用户关注度的目标肯定是达成了。在所有突破中,最令我感到有趣的是关于超级大压铸。而且这也是我写这篇文章的初衷,明明在所有技术亮点中,真正现在就知道小米汽车把事情做对了的就是大压铸,但是就这个话题上大家讨论和关注的点完全不在频道上。事实上在这次发布会之前,我并不知道小米汽车会发布大压铸的技术,鬼使神差的,我在这之前正好发了一个微博对目前中国汽车行业简单粗暴卷压铸的情况吐槽。高压压铸,又叫做HPDC(High Pressure Die Casting),结构简图如下金属首先在熔炼炉中熔化,经过调质、除渣、排气等工序,然后转移到保温炉中,然后倒入压射套筒中。融化的铝合金注入套筒,封闭端口,然后活塞推动快速高压的将铝合金金属流液注射入模具中。为什么要有高压的加压部分呢?可以看看传统的重力铸造,金属流液依靠重力作用来填充整个模具,因此金属的流动与冷却速度、冲型效果、浇注速度都受到了影响。尽管我们可以通过采用惰性气体氛围和模具排气结构来优化,但是重力铸造依然还是只能为体积比较小、结构相对简单的铸造零件服务。而高压铸造适合制造体积较大,结构复杂,表面质量要求高、批量制造速度快的零件。传统的发动机缸体、缸盖、平衡轴壳体等零件都是采用高压铸造工艺。而真实的压铸机可看如下:过去汽车行业的压铸机一般来说在1000-4000吨范围。特斯拉采用的压铸机,压铸机锁模力达到了6000吨,其发布的时候是当时世界上汽车领域高压铸铝锁模力最大的应用。这次小米发布的是9100吨锁模力的压铸机,是目前已经用于制造汽车行业成品的最大锁模力的压铸机了。很多人在纠结这个9100吨和其他企业发布的9000吨的差别。但是Jacky想说的是,这根本就不是重点。真正的重点在这里:为什么这么说?在特斯拉证明了一体式压铸的可行性后,在过去几年,不断有新的主机厂,尤其是新势力车企冲击一体式压铸,但是更多的时候其实依赖的就是本土设备供应商不断投资开发一体式压铸设备之后直接去使用而已。在这个过程中,为了能够不断的扩大压铸锁模力也成为一种军备竞赛的方向。理由也很简单,更大的锁模力就意味着可以把铝液推动到更加复杂结构之中,同时可以让铝液的流动速度更快,从而可以让铝液在更高的温度下就可以完成对模具的填充。所以,似乎一体式压铸的范围越大,锁模力越高,就一定等于压铸的技术更高。那么我要说的是,这种观点显然是错误的。基于高压铸铝一体式铸造的难点所有铸造形式对比锻造、冲压都有成本优势,无论是从材料利用率、材料成本还是工艺成本的角度,更何况取代是激光焊接工艺,而且还是小部件激光焊接。根据我的经验,以任何形式的铸造零件取代锻造和冲压零件或组合零件的成本改进都在30%-55%左右。然而,高压铸造形式上的简单无法掩盖其工艺设计的复杂。首先,结构越复杂,薄壁结构或者壁厚变化结构越多的,越难以实现良好的冲型这张图是高压铸造过程中金属流液的流动分析,可以想象,流动通道越复杂,存在边角结构越多的,就会导致金属在冲型过程中没法良好填充,甚至出现由于流动速度快,形成紊流的情况。而所谓紊流就会导致内部严重的缺陷。流动问题还会带来杂质和氧化皮的风险,流动性不足或由于多处的流动进度不同,从而出现多处金属液面冲击融合,都会导致杂质不能顺利的排出,或者出现氧化皮冷隔。这些都会导致零件失效。然后,接下来的问题就是排气。这里的“气”,既有模具中原来有的气体,也有金属流液自身带进去的气体,还有包含在金属中的气体。铝合金液在一开始熔炼转移到保温炉前就要做好除渣排气的工作,完全的沉淀铝液中的杂质和排出气体,我们会采用取样密度法来评估含气量。然后通过压铸设备的设计来尽可能减少浇注气体,然后到了模具里面,根据仿真结果和填充结构,在模具上还有设置合理的排气结构排出气体,更先进的做法需要采用真空技术来实现。在这里,大量的仿真技术和生产过程控制会被介入。第三,冲型和排气做好了,冷却又是个大问题。冲压是一个冷过程,而铸造是一个热过程。这里面有一个热胀冷缩的问题。我们要准确的仿真铸造零件的完整的冷却过程,而且还要让零件按照我们的想法去冷却。因为冷却就意味着收缩,如果此时没有足够的液态的金属去补缩,那么你就又会出现缺陷。所以我们要让那么大的一个零件按照我们的想法去冷却,还要设置一个最晚冷却的小池子能够补充液体。我们还要避免出现不合群的热孤岛,因为那将会是缺陷生成的起始。而要实现这一点,我们要对零件的铸造特性和热特性了如指掌,而且还要去设计不同的模具冷却方案来进行匹配。在这个过程中,与所有关键环节都相关,并且影响浇铸后成品性能的核心因素就是:材料。我觉得小米汽车在超级大压铸方面至少做对了两件事情:1. 用正确的方法,一开始就明确去卷基础材料开发。之所以前面花了这么大的篇幅去介绍高压压铸的原理和局限性,就是为了在这里解释这一条。一些核心的元素,例如铝、铜、铁、镁、锰等其实是大类合金必定会有的。这里面主要调整的是多种稀土元素和个别稀有元素。这些元素的添加本身就是为了解决前面提到的诸多挑战。主要起到的作用包括:净化铝液的作用:铝在熔炼的过程中,会产生氢、氧、氮等气体,尤其是氢,并融合在铝液之中。添加稀土元素,尤其是Ce(铈读作Shi 四声)和La(镧)等,它们的作用是和氢、氮等形成难以溶解的化合物,然后作为渣的形式沉淀出来。此外,还有硫、磷、砷等,稀土元素可以和稀土元素形成轻质化合物,漂浮到铝液表面然后被捞走。这些措施都可以让铝合金溶液更加纯净稳定,大幅减少铸造缺陷。变质及细化晶粒效应:主要体现在细化晶枝组织,影响成品的显微结构。这对于铝合金的表面质量的提升非常重要。细化晶粒可以显著的提升铝合金的机械性能,减少起源自缺陷进一步开裂的风险。进一步强化效应:稀土元素还有助于与铝合金形成微合金化等效应,进一步提升铝合金的机械性能。这就是我前面微博说的,一上来就卷压机规模是错误的。因为直接卷的压铸机就是简单的砸钱规模放大。真正要解决的是协同的材料突破。小米自研大压铸中最重要的一环就是材料研究,这样自信的在首页就公开具体的成分细节,其实也是因为小米汽车已经申请了这种材料牌号的专利。关于配方这里,我的解读是这样的:1016万种应该指的是开发过程中选型阶梯的理论组合数,1016万开11次方就是4.34,大概就是11种元素小米和合作科研机构平均有4种以上的配比方案,然后首先基于材料学模型进行初步选优。所谓多元仿真,是要兼顾结构强度、铸造流动性、清净性、冷却特性、结构韧性、稳定性等多种因素,进行综合评估。然后选出小范围选型样品后,进行实物浇铸测试。实践证明,选择正确的材料,可以令铸造合格率提升超过30%以上,并显著影响机械性能。2. 没有冒进做底盘、车身大范围一体式压铸。结合式结构更符合一体式压铸的未来。在大型压铸机的加持下,很多企业已经不满足于后地板,而是扩大到了底盘和车身更多的结构上。现在甚至有通过组合后,声称对后车体等更大范围进行一体化铸造的。然而据我了解,其实际铸造报废率的问题一言难尽。一体化铸造可以降低成本,加快节拍。但是设备一次性投入大,售后的事故后如果受损,可维护性差。而铸件的内部缺陷是极难发现的,必须采用大规模无损探伤技术,例如大功率工业CT、X光和超声波设备进行结合检测(按照效果由好到差排序)。尤其是工业CT最可靠,但是成本极为高昂。所以我们经常会看到一家企业在铸造类领域投入大量资金,但是由于基础研究不够,缺陷报废率居高不下,情急之下就会放宽检测标准,让这类产品流入市场。更复杂的结构和更多的薄壁和分支的结构,会导致模流设计和量产稳定性的挑战越来越大。这是一直在局限一体式压铸技术发展的瓶颈。目前来说,小米做的这个后地板的这个尺寸,是一个比较成熟的范围。我个人一直反对无意义的扩大规模,而应该先把现有的范围做到精益。这次小米汽车做的这种基于一体式压铸的结合式结构让我觉得很有趣,即实现了集成性,又将压铸件保持在结构内部,在小规模碰撞的时候可以以可拆卸替换的结构避免整车更换。这类思考也确实有利于大家思考如何有效的结合不同技术的优劣以及最大化的满足客户利益。以上,就是我这次看到的小米汽车大压铸的一点感想。可能扯得有点远,但是我觉得有助于讨论和思考一些真正有助于行业发展方向技术点。小米汽车具体表现如何,还要等待几个月后的正式发布,不过我想说,它确实引起了我的注意。 来源:知乎 www.zhihu.com 作者:JackyQ 【知乎日报】千万用户的选择,做朋友圈里的新鲜事分享大牛。 点击下载 此问题还有 276 个回答,查看全部。 延伸阅读: 小米首款汽车SU7搭载的核心部件及技术是否先进?有哪些值得关注的点? 驾驶小米 SU7 汽车的感受是什么?
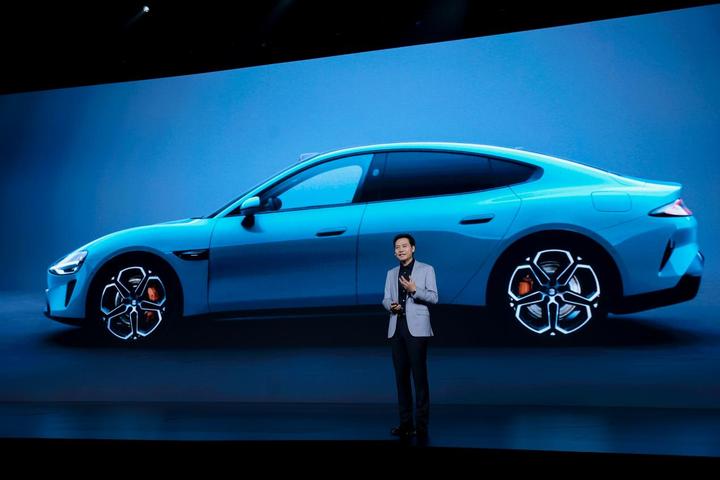
雷军在本周发布了小米汽车的技术发布会,展示了包括在电驱、电池、大压铸、智能驾驶、智能座舱五个核心领域的突破和主要技术要素。这些相关议题连续霸榜了多日多平台的热搜头条。
可惜我作为一个汽车产业的技术人员,这个时候的主要工作是做年底总结和新年计划,所以到今天这个假期,才有机会聊一聊小米汽车的这场技术展会。
在过去的几天很多媒体、技术人员甚至主机厂的高管都加入到了这些技术亮点的讨论,有认可小米汽车亮点优势的,当然也有认为这里面依托了很多是供应商的技术突破,从而对小米汽车的自称自研颇有微词。关于这一点,我想说的是:
- 新技术上限刷新的前提,首先来自于主机厂的产品定义。例如现在说到的高速电机,首先来自于小米对于su7的定义是要实现赛道级265kph的高速,那么在相同的结构下,更高的车速需求就需要电机适应更高的转速,除非你设置更加复杂的多挡结构。这是促使小米汽车去寻找能够支持突破转速上限电机供应商和挖掘自身合作研发实力的原始动力。再比如使用宁德时代麒麟电池倒置布局,其核心目标是在轿跑造型下布置超过100度电池的同时必须满足极限的电池包高度,只有这样才能在离地间隙、车内空间和维持低趴轿跑造型中得到妥协。
- 首发应用,整车集成的联合开发技术难度很多时候不亚于零件自身的突破。简单来说就是第一波趟整车集成标准改变和测试验证的雷的就是首发主机厂。我们也注意到小米对周边技术和具体的方案也进行了大量的知识产权保护的工作,这也从侧面显示出这个是联合开发,而不是简单借用。
所以,我觉得我们更应该关注和讨论的是,电动汽车高达265kph的高速性能冗余对于客户的价值如何挖掘,这种既要维持轿跑和低风阻造型又拼了命去应用最新的技术去挤出空间这种整车定位,是否真正抓住了米粉群体的爽点。所以小米汽车发布之后,我们知乎VIP创作者群里面马上就在艾特社区负责人,赶紧搞一辆知乎体验官试驾,在此我也呼吁小米汽车如果看到这篇文章,请考虑与知乎汽车合作。
我在2019年1月去蔚来汽车内部交流的时候,我问过:为什么你们要首发ES8这款大七座但又续航里程只有355km的车型。因为当时的电池能量密度技术有局限性的情况下,ES8为了满足和后来的ES6共用电池包换电而牺牲了一大块空间闲置。也就是说,明明蔚来可以先首发看起来更加具有性价比的ES6,但是依然决定先冲ES8。蔚来高管的回答其实很直白,正如一开始要先打EP9一样,一个新品牌的首发车型就如同第一印象一样,决定了品牌的格调和定位。
汽车品牌从高端做大众品牌容易,从低端向高端做更难。尤其是对于电动汽车这种破坏性创新的品牌,冲击颠覆高端对于销量的挑战有些大,但是对于品牌长期的价值留下了更大的空间。
由于目前Su7的售价还没有公布,大家还在争议和猜测,但是Su7的赛道级高性能引发的品牌价值塑造和用户关注度的目标肯定是达成了。
在所有突破中,最令我感到有趣的是关于超级大压铸。而且这也是我写这篇文章的初衷,明明在所有技术亮点中,真正现在就知道小米汽车把事情做对了的就是大压铸,但是就这个话题上大家讨论和关注的点完全不在频道上。
事实上在这次发布会之前,我并不知道小米汽车会发布大压铸的技术,鬼使神差的,我在这之前正好发了一个微博对目前中国汽车行业简单粗暴卷压铸的情况吐槽。
高压压铸,又叫做HPDC(High Pressure Die Casting),结构简图如下
金属首先在熔炼炉中熔化,经过调质、除渣、排气等工序,然后转移到保温炉中,然后倒入压射套筒中。融化的铝合金注入套筒,封闭端口,然后活塞推动快速高压的将铝合金金属流液注射入模具中。
为什么要有高压的加压部分呢?可以看看传统的重力铸造,金属流液依靠重力作用来填充整个模具,因此金属的流动与冷却速度、冲型效果、浇注速度都受到了影响。尽管我们可以通过采用惰性气体氛围和模具排气结构来优化,但是重力铸造依然还是只能为体积比较小、结构相对简单的铸造零件服务。
而高压铸造适合制造体积较大,结构复杂,表面质量要求高、批量制造速度快的零件。传统的发动机缸体、缸盖、平衡轴壳体等零件都是采用高压铸造工艺。而真实的压铸机可看如下:
过去汽车行业的压铸机一般来说在1000-4000吨范围。特斯拉采用的压铸机,压铸机锁模力达到了6000吨,其发布的时候是当时世界上汽车领域高压铸铝锁模力最大的应用。
这次小米发布的是9100吨锁模力的压铸机,是目前已经用于制造汽车行业成品的最大锁模力的压铸机了。
很多人在纠结这个9100吨和其他企业发布的9000吨的差别。但是Jacky想说的是,这根本就不是重点。真正的重点在这里:
为什么这么说?
在特斯拉证明了一体式压铸的可行性后,在过去几年,不断有新的主机厂,尤其是新势力车企冲击一体式压铸,但是更多的时候其实依赖的就是本土设备供应商不断投资开发一体式压铸设备之后直接去使用而已。
在这个过程中,为了能够不断的扩大压铸锁模力也成为一种军备竞赛的方向。理由也很简单,更大的锁模力就意味着可以把铝液推动到更加复杂结构之中,同时可以让铝液的流动速度更快,从而可以让铝液在更高的温度下就可以完成对模具的填充。所以,似乎一体式压铸的范围越大,锁模力越高,就一定等于压铸的技术更高。那么我要说的是,这种观点显然是错误的。
基于高压铸铝一体式铸造的难点
所有铸造形式对比锻造、冲压都有成本优势,无论是从材料利用率、材料成本还是工艺成本的角度,更何况取代是激光焊接工艺,而且还是小部件激光焊接。根据我的经验,以任何形式的铸造零件取代锻造和冲压零件或组合零件的成本改进都在30%-55%左右。
然而,高压铸造形式上的简单无法掩盖其工艺设计的复杂。
首先,结构越复杂,薄壁结构或者壁厚变化结构越多的,越难以实现良好的冲型
这张图是高压铸造过程中金属流液的流动分析,可以想象,流动通道越复杂,存在边角结构越多的,就会导致金属在冲型过程中没法良好填充,甚至出现由于流动速度快,形成紊流的情况。而所谓紊流就会导致内部严重的缺陷。流动问题还会带来杂质和氧化皮的风险,流动性不足或由于多处的流动进度不同,从而出现多处金属液面冲击融合,都会导致杂质不能顺利的排出,或者出现氧化皮冷隔。这些都会导致零件失效。
然后,接下来的问题就是排气。
这里的“气”,既有模具中原来有的气体,也有金属流液自身带进去的气体,还有包含在金属中的气体。铝合金液在一开始熔炼转移到保温炉前就要做好除渣排气的工作,完全的沉淀铝液中的杂质和排出气体,我们会采用取样密度法来评估含气量。然后通过压铸设备的设计来尽可能减少浇注气体,然后到了模具里面,根据仿真结果和填充结构,在模具上还有设置合理的排气结构排出气体,更先进的做法需要采用真空技术来实现。在这里,大量的仿真技术和生产过程控制会被介入。
第三,冲型和排气做好了,冷却又是个大问题。
冲压是一个冷过程,而铸造是一个热过程。这里面有一个热胀冷缩的问题。我们要准确的仿真铸造零件的完整的冷却过程,而且还要让零件按照我们的想法去冷却。因为冷却就意味着收缩,如果此时没有足够的液态的金属去补缩,那么你就又会出现缺陷。所以我们要让那么大的一个零件按照我们的想法去冷却,还要设置一个最晚冷却的小池子能够补充液体。我们还要避免出现不合群的热孤岛,因为那将会是缺陷生成的起始。
而要实现这一点,我们要对零件的铸造特性和热特性了如指掌,而且还要去设计不同的模具冷却方案来进行匹配。
在这个过程中,与所有关键环节都相关,并且影响浇铸后成品性能的核心因素就是:材料。
我觉得小米汽车在超级大压铸方面至少做对了两件事情:
1. 用正确的方法,一开始就明确去卷基础材料开发。
之所以前面花了这么大的篇幅去介绍高压压铸的原理和局限性,就是为了在这里解释这一条。一些核心的元素,例如铝、铜、铁、镁、锰等其实是大类合金必定会有的。这里面主要调整的是多种稀土元素和个别稀有元素。这些元素的添加本身就是为了解决前面提到的诸多挑战。
主要起到的作用包括:
- 净化铝液的作用:铝在熔炼的过程中,会产生氢、氧、氮等气体,尤其是氢,并融合在铝液之中。添加稀土元素,尤其是Ce(铈读作Shi 四声)和La(镧)等,它们的作用是和氢、氮等形成难以溶解的化合物,然后作为渣的形式沉淀出来。此外,还有硫、磷、砷等,稀土元素可以和稀土元素形成轻质化合物,漂浮到铝液表面然后被捞走。这些措施都可以让铝合金溶液更加纯净稳定,大幅减少铸造缺陷。
- 变质及细化晶粒效应:主要体现在细化晶枝组织,影响成品的显微结构。这对于铝合金的表面质量的提升非常重要。细化晶粒可以显著的提升铝合金的机械性能,减少起源自缺陷进一步开裂的风险。
- 进一步强化效应:稀土元素还有助于与铝合金形成微合金化等效应,进一步提升铝合金的机械性能。
这就是我前面微博说的,一上来就卷压机规模是错误的。因为直接卷的压铸机就是简单的砸钱规模放大。真正要解决的是协同的材料突破。
小米自研大压铸中最重要的一环就是材料研究,这样自信的在首页就公开具体的成分细节,其实也是因为小米汽车已经申请了这种材料牌号的专利。
关于配方这里,我的解读是这样的:1016万种应该指的是开发过程中选型阶梯的理论组合数,1016万开11次方就是4.34,大概就是11种元素小米和合作科研机构平均有4种以上的配比方案,然后首先基于材料学模型进行初步选优。所谓多元仿真,是要兼顾结构强度、铸造流动性、清净性、冷却特性、结构韧性、稳定性等多种因素,进行综合评估。然后选出小范围选型样品后,进行实物浇铸测试。
实践证明,选择正确的材料,可以令铸造合格率提升超过30%以上,并显著影响机械性能。
2. 没有冒进做底盘、车身大范围一体式压铸。结合式结构更符合一体式压铸的未来。
在大型压铸机的加持下,很多企业已经不满足于后地板,而是扩大到了底盘和车身更多的结构上。现在甚至有通过组合后,声称对后车体等更大范围进行一体化铸造的。然而据我了解,其实际铸造报废率的问题一言难尽。
一体化铸造可以降低成本,加快节拍。但是设备一次性投入大,售后的事故后如果受损,可维护性差。而铸件的内部缺陷是极难发现的,必须采用大规模无损探伤技术,例如大功率工业CT、X光和超声波设备进行结合检测(按照效果由好到差排序)。尤其是工业CT最可靠,但是成本极为高昂。所以我们经常会看到一家企业在铸造类领域投入大量资金,但是由于基础研究不够,缺陷报废率居高不下,情急之下就会放宽检测标准,让这类产品流入市场。
更复杂的结构和更多的薄壁和分支的结构,会导致模流设计和量产稳定性的挑战越来越大。这是一直在局限一体式压铸技术发展的瓶颈。目前来说,小米做的这个后地板的这个尺寸,是一个比较成熟的范围。我个人一直反对无意义的扩大规模,而应该先把现有的范围做到精益。
这次小米汽车做的这种基于一体式压铸的结合式结构让我觉得很有趣,即实现了集成性,又将压铸件保持在结构内部,在小规模碰撞的时候可以以可拆卸替换的结构避免整车更换。这类思考也确实有利于大家思考如何有效的结合不同技术的优劣以及最大化的满足客户利益。
以上,就是我这次看到的小米汽车大压铸的一点感想。可能扯得有点远,但是我觉得有助于讨论和思考一些真正有助于行业发展方向技术点。小米汽车具体表现如何,还要等待几个月后的正式发布,不过我想说,它确实引起了我的注意。
来源:知乎 www.zhihu.com
作者:JackyQ
【知乎日报】千万用户的选择,做朋友圈里的新鲜事分享大牛。
点击下载
此问题还有 276 个回答,查看全部。
延伸阅读:
小米首款汽车SU7搭载的核心部件及技术是否先进?有哪些值得关注的点?
驾驶小米 SU7 汽车的感受是什么?


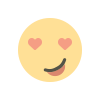


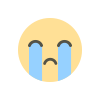
